过去两年(2015 年和 2016 年)可谓是航天行业直接金属打印 (DMP) 的转折点,这两年中,该技术逐渐超越原型制造阶段,进入了飞行就绪的生产部件和装配阶段。
在此期间,空中客车集团防务与航天公司与 3D Systems 合作,实现重大突破:首个适用于商业通信卫星的 3D 打印射频滤波器 (RF) 已经过测试和验证。该项目的开展基于欧洲空间局 (European Space Agency) 所资助的研究(A0/1-6776/11/NL/GLC:利用 3D 制造技术对优化的波导元件进行建模和设计)。
金属射频或波导滤波器的使用可追溯到近 50 年前的第一个航天通信系统。滤波器的作用类似于交通警察,允许来自指定频道的频率通过,拒绝来自这些频道之外信号的频率。
如今的主要工业趋势是增加单个卫星内多个波束的容量。空中客车集团防务与航天公司制造的 Eutelstat KA-SAT 等高容量卫星配备了近 500 个射频滤波器和 600 多个波导滤波器。其中有许多经过了自定义设计,以处理特定频率。
符合临界要求
通信卫星体现了航天行业对减轻重量的不懈努力 — 将一个太空车送入地球静止轨道的成本可高达每公斤 20,000 美元。持续的设计创新和缩短生产时间也是需要优先解决的重要挑战,因为大多数卫星的设计使用寿命是 10–15 年。
由于这种优先性,通信卫星也是直接金属打印的理想选择。Airbus 射频滤波器项目使用的 3D Systems ProX® DMP 320可帮助制造商整合部件;利用无法以传统方式制造的形状和表面来改进功能;缩短生产时间,从而降低定制设计成本;以及减轻重量,同时保持或改进材料强度。
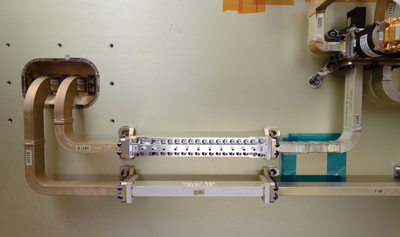
经过验证的打印机适用的新应用
自 3D Systems ProX DMP 320 进入测试阶段以来,3D Systems 位于比利时鲁汶的设施就一直使用该设备。成功的项目包括经航天验证的部件(例如通信卫星的支架和支撑件装置)的优化拓扑构造、减重和部件整合。空中客车集团防务与航天公司的项目是 3D Systems 鲁汶公司首次涉足射频滤波器。
ProX DMP 320 旨在于严苛的 24/7 全天候生产环境中实现高精度和高吞吐量。其丰富多样的 LaserForm 合金(钛、不锈钢、铝、镍铬和钴铬)经过特殊配方和精调以用于该金属打印机,从而生产高质量部件并实现属性一致。
在更换不同的部件材料时,可交换式制造模块进一步提高了应用灵活性,并且减少了停机时间。受控的真空构建室可确保每个部件均利用经验证的材料属性、密度和化学纯度进行打印。
颠覆性设计创新
空中客车集团防务与航天公司射频滤波器项目体现了 3D 打印的强大能力,对于数十年间未发生明显变化的航天部件而言,3D 打印有助于实现此领域的新设计创新。
传统而言,射频滤波器的设计基于标准元素库,例如矩形空腔和具有矩形弯曲的波导横截面。形状和连接取决于典型制造过程,例如铣削和火花塞蚀刻。因此,用于射频滤波器的空腔通常需要通过螺栓将两半部件固定加工而成。这就增加了整体重量,增加了装配时间,从而增加了生产时间,并且需要额外的
质量评估步骤。
设计可用于 3D 打印的部件,这能帮助空中客车集团防务与航天公司探究复杂的几何形状,同时不产生额外的制造成本。
CST MWS 是标准的 3D 电磁模拟软件工具,该工具常用于设计 3D 打印射频滤波器,并且仅需花费较少时间进行优化。使用 3D 打印可增加制造灵活性,从而可利用凹陷的超椭圆空腔来完成设计。这种独特的形状有助于引导射频电流,以及在 Q 因子(这是基于能量损失的波导效率度量)和
带外信号的抑制之间进行平衡。
“颠覆性的创新在于,其纯粹的功能性,而非可制造性,现在决定了硬件的设计方式,”鲁汶 3D Systems 的项目工程师 Koen Huybrechts 说道。“这个项目是‘构型遵循功能’的典型示例。”
“通过 3D 打印实现的一体式设计的主要优势在于质量轻、成本低和时间短,”英国斯蒂夫尼奇空中客车集团防务与航天公司的射频工程师 Paul Booth 说道。“由于不再需要紧固件,因此,质量得到了减轻。利用直接金属打印,还有一个好处就是,外部轮廓能更紧密地贴合内部轮廓,因此,只需要使用真正必要的金属材料即可,无需额外成本。由于减少了装配和后处理过程,因此,成本/时间也得以减少。”
消除曲面问题
最初,3D 打印金属部件的不同曲面拓扑构造通常被视作问题所在,但 空中客车集团防务与航天公司进行的广泛测试消除了这些问题。
“3D 打印部件的微观拓扑构造与机械加工部件不同,”Booth 说道,“机械加工的曲面有尖锐的凸起和凹陷,而 3D 打印的曲面是将类球面熔合在一起,因此锐边较少。”
“3D 金属打印所使用的粉末颗粒为球形,这会产生一定的波纹,而不是凹凸不平的过渡,”Huybrechts 说道,“但是,部件形状能否实现更有效的信号过滤比能否克服与曲面拓扑构造相关的问题更重要。”
“我们很满意 3D Systems 为我们提供的帮助,并且 Airbus 内部的许多人员都对表面光洁度作出了很高的评价,”Booth 说道,“我们进行了 X 光 CT 扫描,并且对部件的密度十分满意,整体曲面质量也十分卓越。”
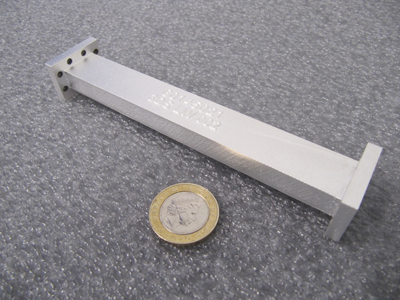
通过严格的测试
在 ProX DMP 320 中利用不同的处理方式所打印的三个铝样品已由空中客车集团防务与航天公司在其斯蒂夫尼奇的设施进行了测试。测试模拟了部件在发射和轨道运行期间面临的环境,包括振动、冲击、热环境(如极端温度)和真空环境。这三个样品均达到或超过要求,其中性能最佳的是经过电解处理的镀银滤波器。
除了 3D 打印,3D Systems 还提供对于此类项目而言至关重要的附加价值,包括经认证的粉末处理、旨在实现卓越材料密度的过程控制、经验证的后处理,以及可靠的质量控制。
Booth 意识到,这种附加的专业能力对项目的成功而言十分重要:“我们发现,成功的秘诀不仅仅是使用优质的机械来制造部件,也是 3D Systems 透彻了解制造过程的结果。”
巨大的投资回报率潜力
随着制造流程经过验证,并且部件已经达到 空中客车集团防务与航天公司制定的最高航天标准,该公司已可以开始考虑 3D 金属打印的潜在投资回报率。该项目的投资回报率定能让公司首席财务官眼前一亮:周转时间更快、生产成本更低,并且重量减少高达 50%。
“无需花费额外的时间进行优化即可实现减重,”Booth 说道,“通过更先锐的机械设计还可以实现进一步减重。质量减轻则意味着火箭中需要的推进剂更少,从而有助于减少成本,并且对支撑结构的需求也减少了,从而进一步减轻了质量。
“这个项目的成功推动了更理想的射频滤波器与机械和热组件集成方式,从而减少部件数量和整体质量。我们还将研究如何集成更多功能,例如测试耦合器作为滤波器的一部分,或直接集成到波导滤波器运行中。在减少质量同时缩短生产时间并降低成本方面,我们仍有巨大空间。”